Weaving in indigenous Dimasa community of Assam
19 December 2019, by Avantika Haflongbar
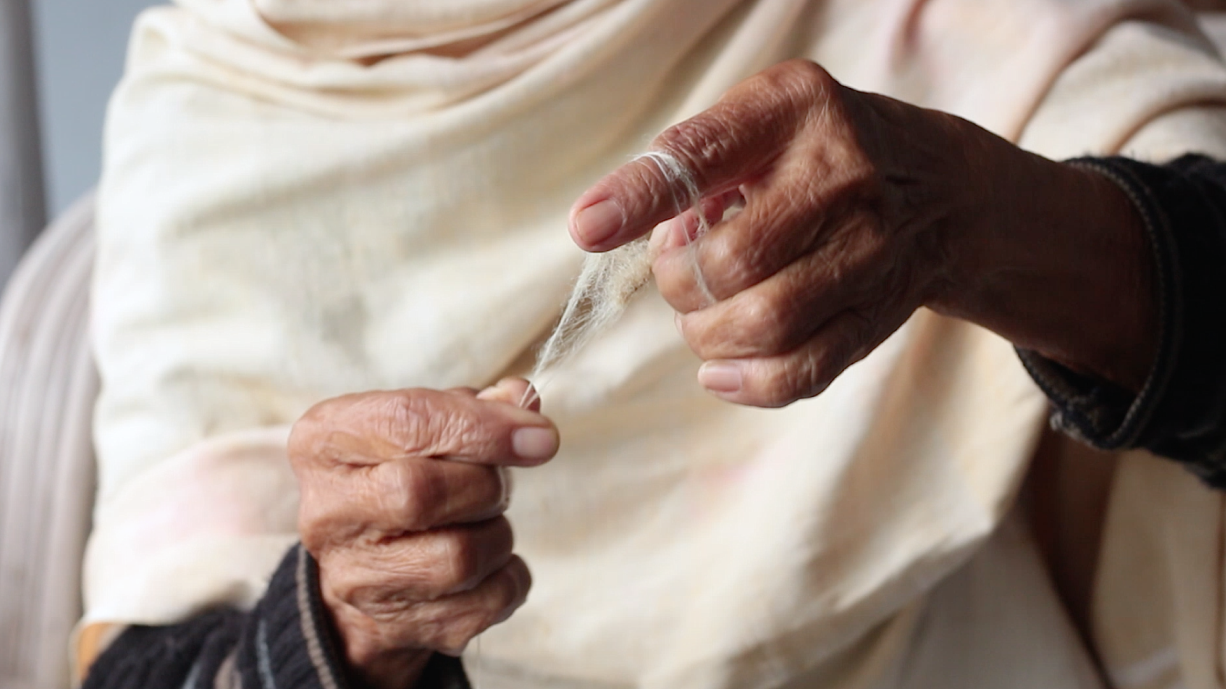
Eri rearing is an age old tradition of the Dimasa women. Process of rearing eri worms is usually carried out in March-April and September-October, the most suitable seasons for its rearing. The women folk rear ‘yungma’ (silkworm, eripolu) to produce ‘khunthon’ (eri/ endi silk) and the cloth produced from this thread is called ‘rihendi’. Eri silkworm feeds on castor leaves and kesseru leaves, which are majorly found in Dima Hasao district. Castor leaves are known as ‘Radaolai’. It takes one month to complete a cycle of re-rearing, from egg larva to cocoon. At a certain time, the eri moth leaves the cocoon on its own. Eri silk spinning does not involve the killing of the silkworm. Hence, eri silk is known as Ahimsa silk or non-violence silk. Before spinning, the eri cocoons are boiled in ‘khari’, an alkali mixed with water, for around an hour. The khari used for boiling the eri cocoon is made from the charcoal of the castor stem. It is different from the other khari made from banana-stem ash. After boiling, the cocoons become thin. These are later dried in the sun and kept aside for spinning. The method of reeling is known as ‘thakriluba’ and the ball of endi/ eri thread is called ‘khunthon’. For spinning the khunthon, a special tool known as ‘thakri’ (spindle) is required. The main fabric traditionally made by eri yarn is a shawl called ‘rihthap’.
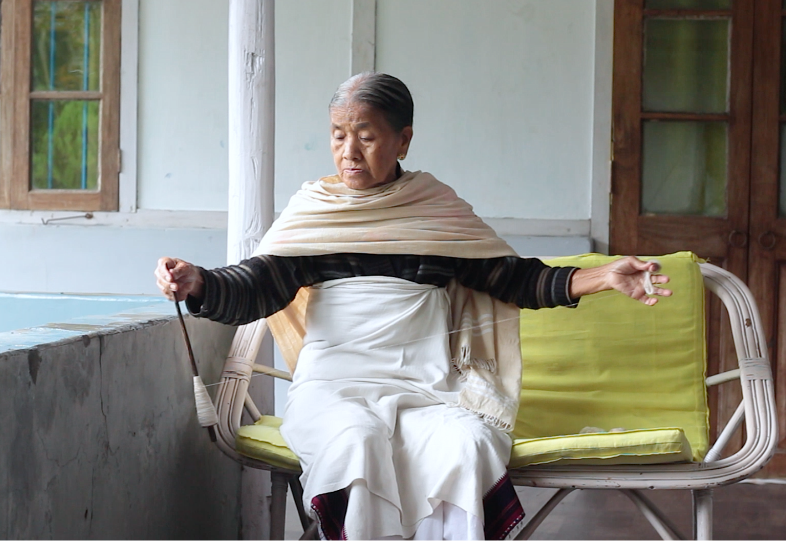
The Dimasa people conserved the khunphang/ cotton plant for weaving. In earlier days, it used to be cultivated in ‘jhum’ (slash-and-burn) method of farming land along with other crops. Previously, Dimasa women used to do cotton ginning in their homes, then spin it on spinning wheels. But in the recent past, cotton cultivation amongst the Dimasa community is on a decline. The yarn produced from cotton is called ‘khundi’and the process of spinning the cotton is known as ‘khundi luba’.
Dimasas use plants as natural dye to colour their cotton yarns. They carry on the process of dyeing twice a year. They prepare red dye from the root of a wild raw indigo plant known as ‘jengklong’ and the method of dyeing black colour is prepared from the leaves of wild herbs known as ‘gisim balai’. The dyeing process is generally done in winter. Before the yarn is dyed, it has to be kept out in the open at night for about a week. When the yarn becomes completely moist with dew, it is ready for dyeing. But this practice is on the verge of extinction and naturally dyed cotton yarns have been replaced by readymade multi-coloured acrylic yarns.
All the Dimasa designs, known as ‘rikhu’, before being woven in the fabric, are carried out in the traditional device known as ‘gonthai’. We generally use ‘wahdu ni gonthai’ (gonthai made of thread). This kind of gonthai is made by cutting two hard bamboo sticks, vertically tying it with endi/ eri thread in 37 lines where, different colours of thread are allowed to hang horizontally. The horizontal colours of thread represent different rikhu.
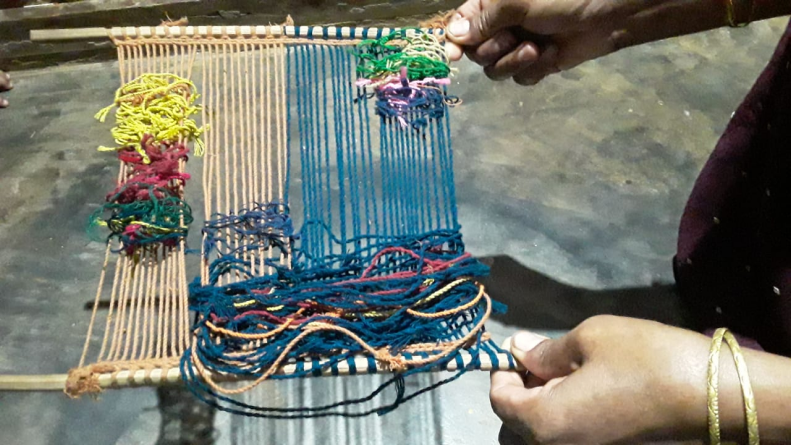